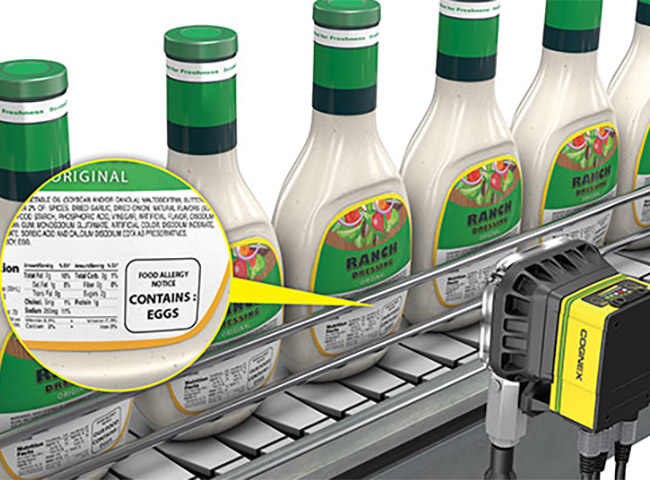
Cognex Product Traceability: Increasing Production Efficiency through Product Tracking
Many complex systems, such as automobiles, contain thousands of parts created by individual manufacturing facilities around the world. All of these parts have to work flawlessly in concert, and the failure of one part can mean failure of the whole system. Manufacturers want to be able to guarantee the quality of their individual parts and to trace the life cycle of those parts from manufacturing through installation and operation. Traceability processes allow manufacturers to ensure this quality.
Traceability Starts at the Factory
There are two general methods of instilling traceability on manufactured parts: barcodes or alpha numeric codes. These identification codes can be printed on labels that are affixed to a part or alternatively printed or engraved directly on the part. Directly adding identification codes to a part ensures that the code remains on the part even if a label is lost over time. These codes often include information on the model number and serial number of the part, factory information, date of manufacture, and other information relevant to that part.
Tracing Parts with Automated Vision Systems
Imprinting a part with an identification code is only the beginning of instilling traceability. The code on each and every part has to be read at each point in the manufacturing, assembly, and testing operation to track the location and performance of that part. Codes can be read as a part is picked for assembly, inspected for quality, or tested for performance. The codes are used by the manufacturing system to determine exactly where each part is in the factory, and verifies when it exits the line.
To read these identification codes, an automated vision system is used, such as the In-Sight® 5110 vision system from Cognex, along with their VisionPro® software. These systems can image the part, locate the identification code and look up the code in the system database. The software then updates the database with the current location of that individual part.
Automated vision is not limited purely to identification. These systems are integrated with inspection and testing processes, allowing the system to annotate the part database with information on inspection pass/fail, test results, and the location of the part, which could vary depending on the results of inspection or testing. Vision systems are also used to verify the quality of the traceability process. After a part is imprinted with a code, a vision system is generally used to image the code right away to ensure that it can be clearly read and the number can be entered into the manufacturing database.
Parts that do not pass testing or inspection can be directed to a different part of the factory to be manually inspected so operators can determine if the part is inherently faulty or if it can be repaired. Identification codes can even be used to troubleshoot faulty systems later in the product lifecycle. By reading an identification code, all of the processes that part underwent in the manufacturing facility can be called up with a single database command.
Ensuring Quality of Traceability Processes
Because these identification codes are read at different inspection stations and potentially different facilities altogether, the vision systems need to be capable of reading these codes under varying environments. Parts could be coated in grease after assembly, yet the vision systems need to be able to accurately read the identification code. Lighting is key to vision readability, and adequate lighting must be installed at each inspection station. The vision system hardware and software needs to be flexible enough to adapt to varying lighting conditions and product orientations.